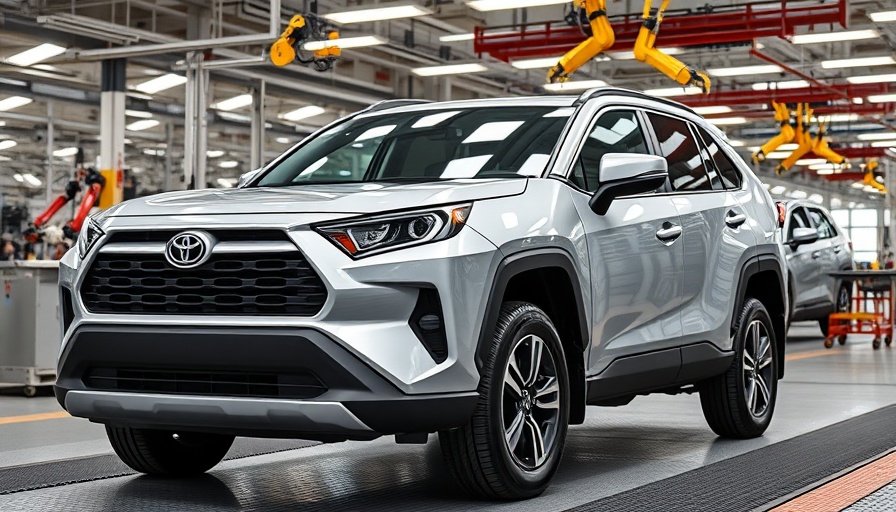
A Devastating Incident Shakes Toyota's Production
On March 6, 2025, a tragic explosion at a parts supplier factory in Toyota City, Japan, has brought production of the RAV4 and other models to a halt. The explosion claimed the life of one worker and injured two others, leading Toyota to pause operations across three production lines at two different plants. The immediate focus has been on the safety of workers and the evaluation of the supply chain's integrity.
What Does This Mean for RAV4 Supply?
The RAV4, a popular SUV in the United States, accounts for a significant portion of sales, with approximately 21% of the 475,193 RAV4s sold last year being imported from Japan. The current halt, compounded by the tragic incident, raises concerns about inventory levels and delivery timelines. While Toyota has stated that it's too early to determine the exact impact on U.S. shipments, the potential for delays looms large.
The Ripple Effects on the Automotive Industry
This incident is not isolated; it reminds us of past events that have disrupted automotive production lines. A similar explosion at a supplier in October 2023 forced Toyota to close eight plants, resulting in a 10-day interruption of production. These recurring disruptions highlight vulnerabilities in automotive supply chains during crises. As companies increasingly rely on just-in-time manufacturing techniques, incidents like these can have widespread impacts.
Safety First: The Response to the Crisis
Following the explosion, various stakeholders in the automotive sector have expressed their concerns. Safety protocols in supplier companies are under scrutiny, emphasizing the need for stringent regulations to protect workers. The automotive industry is key to Japan’s economy, and ensuring the safety of those who keep it running is paramount.
Looking Ahead: The Future of the RAV4 Production
As Toyota plans to reassess operations on March 11, industry analysts are watching closely for updates on the production status of the RAV4 and its potential impact on North America. With the company's reputation for reliability on the line, timely communication with consumers and dealerships will be crucial in maintaining trust.
What Can Dealers Do in Response?
This incident serves as a critical reminder for dealership owners and general managers about the importance of supply chain management and proactive communication. As potential delays unfold, dealerships must prepare to manage customer expectations and provide alternatives to affected clients. Building a strong relationship with customers can foster loyalty, even during challenging times.
In light of the unfolding situation, dealership personnel should stay informed and ready to communicate updates to customers effectively. Whether by providing potential wait times or detailing available inventory from other regions, proactive engagement will be essential in mitigating concerns.
If you're looking for practical insights into how to handle these types of supply chain disruptions, we invite you to check out our resources at DealerSuccessPlaybook.com for expert advice tailored specifically to dealership strategies.
Write A Comment