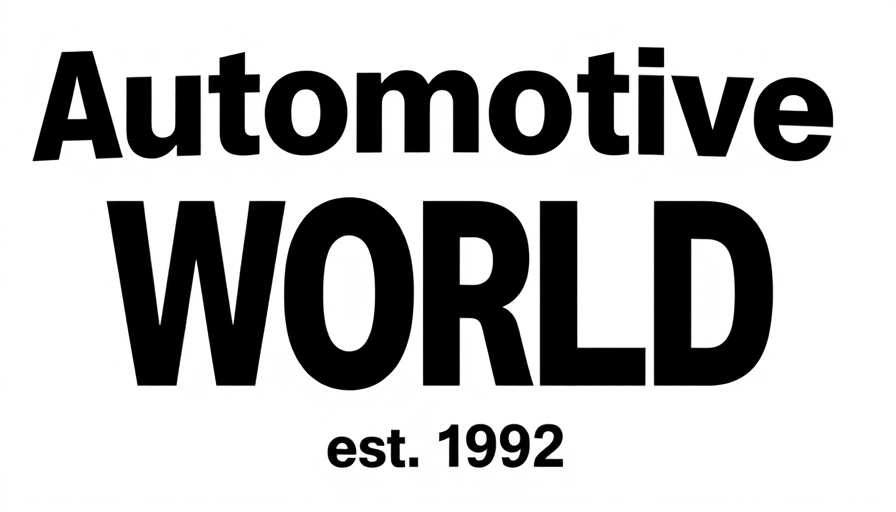
Partnership Paving the Way for EV Battery Production
In a significant move for the electric vehicle (EV) industry, Schneider Electric has forged a partnership with Liminal Insights to tackle ongoing challenges in battery manufacturing. This partnership comes at a crucial time as demand for EV batteries skyrockets, with projections indicating that global EV sales will reach 40% by 2030. As electric vehicles replace internal combustion engines, manufacturers are pressed to scale operations while minimizing waste and improving quality.
Challenges in EV Battery Manufacturing
Currently, battery manufacturers face substantial obstacles in achieving efficiency in production. Scrap rates in mature battery factories rise between 6% and 15%, often due to late identification of quality issues. This not only hampers profits but extends lead times, complicating efforts to meet growing demand. As regulators push for a swift transition to sustainable transport, the partnership between Schneider Electric and Liminal offers a potential remedy.
Innovative Inspection Technology: The EchoStat Advantage
One of the cornerstones of this collaboration is the introduction of Liminal's EchoStat ultrasound inspection solution, designed to identify production deviations in real-time. This technology integrates seamlessly with Schneider Electric's automation systems, allowing for the early detection of quality issues—an essential feature given the hefty estimated cost of recalls in the battery industry that reached over $3 billion from 2020 to 2023.
The EchoStat system's ability to detect a mere 1% reduction in scrap can equate to average savings of $10 million for a standard 10 GWh production block. Moreover, streamlining the cell-finishing process can yield additional savings of up to $3 million annually.
The Future of Sustainable Manufacturing
This partnership signifies a commitment to future-proofing battery production operations by ensuring that manufacturers can adapt to various battery chemistries. The flexibility of the EchoStat solution allows battery manufacturers—regardless of their production scale—to implement a standardized approach to inspection, thereby improving overall quality and safety across the production line. Unlike traditional X-ray technologies, the ultrasound method offers a radiation-free environment, thus simplifying compliance requirements while fostering a safer workplace.
What This Means for the Automotive Industry
The implications of this partnership are profound, not only for battery manufacturers but for the automotive industry at large. As electric vehicles gain more traction, the ability to produce high-quality batteries efficiently will define the competitive landscape. By minimizing waste and enhancing production quality, Schneider Electric and Liminal’s joint efforts may soon set new benchmarks for battery manufacturing.
With the automotive sector rapidly evolving, the need for scalable and sustainable production solutions is more critical than ever. As this partnership unfolds, it may well provide a blueprint for how other industries can leverage technology to confront their own manufacturing challenges.
Write A Comment